Wire rope has a wide range of uses and performs critical functions in many fields, such as the aerospace, marine, construction and defense industries. However, wire rope is also susceptible to corrosion which affects individual strands, weakening the overall assembly below its rated weight capacity, and affecting its performance and safety. Wire rope corrosion can happen for several reasons, such as:
- Oxygen: The steel or other metals comprising the wire rope strands react with oxygen when exposed to air, creating rust.
- Salt: Particularly in marine environments, the salt in the water reacts with the metal to rust and corrode the wire strands.
- Chemicals: In industrial settings, some chemicals will react differently with various wire rope assemblies.
- Abrasion: Dust, grit or cuttings can get between wire rope strands, either abrading the strands themselves or cutting the covering protecting the wire rope from oxygen or seawater.
- Stress: When two different types of steel or metal come into contact, reactions can happen due to differing chemical compositions, often in combination with other elements, which leads to one corroding the other.
The Impact of Wire Rope Corrosion
Corrosion over time is the biggest threat to the stability and continued rated function of wire rope. This manifests itself in several ways, including:
Stiffness
Corrosion, rust and the changed chemical composition of wire rope increase stiffness and reduce its maneuverability and flexibility. This can be due to the stiffness of the wire strands themselves or a build-up of rust at particular points inside the wire rope assembly.
Wire Strand Damage
Corrosion will likely affect multiple points along a wire rope assembly, causing small amounts of damage or abrasion. Over time these effects will accumulate at particular stress points and even cause individual strands to snap, putting more load on the rest of the strands. This significantly reduces the lifespan and functionality of the wire rope.
Weakened Capacity
The rated weight capacity for wire rope is essential for most of its functions, such as lifting and pulling. Corrosion of individual strands weakens the assembly’s load-carrying capacity. This poses a significant safety risk and can lead to sudden cable snapping.
How Wire Rope Corrosion is Minimized
To increase the lifespan of wire rope at its rated strength, steps are taken at the manufacturing and ordering stages to minimize potential wire rope corrosion. The primary methods of reducing wire rope corrosion include:
Lubrication
To protect against wire rope corrosion and friction, as the strands inside the rope roll over each other, the individual strands and the final rope run through a lubricant during manufacturing. Some common lubricants include petrolatum compounds, asphaltic compounds, and various types of grease with sodium or lithium thickeners.
- The term “bright” wire rope refers to plain carbon steel wire rope that has been lubricated. “A” lube is the lightest and standard default for bright wire rope. “B”, “C”, and “D” lubes are used when heavier lubes are required, which is typical in offshore rigging for oil and gas (see API SPEC 9A for more details on wire rope for the petroleum sector).
- Galvanized steel wire rope can be lubricated, but is not always.
- Similarly, stainless steel wire rope can be lubricated, but is not always.
- Military specification aircraft cable such as MIL-DTL-83420 is always lubricated.
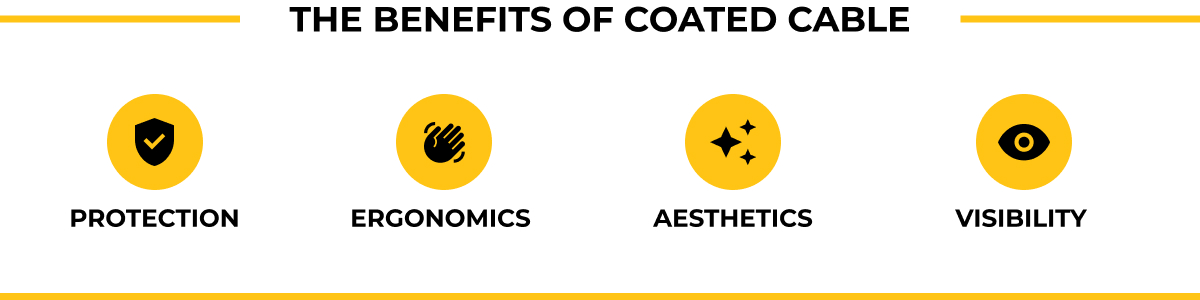
Coating (Jacketing)
Another means of protecting wire rope is coating it in a protective material to both protect the metal and improve the effects of lubrication. The materials used for coating wire rope include polyvinyl chloride (PVC), polypropylene, high-density polyethylene (HDPE), and nylon. The wire rope is generally extrusion coated and pushed through an extrusion machine that coats it to a specific thickness when passing through tooling.
For some extreme environments, cables and wire ropes are offered polypropylene impregnated. This process fills the gaps between the interior wires and strands with plastic. As a result it becomes impenetrable from air and moisture.
Galvanized Finish Steel
Another method for protecting carbon steel wire rope is by applying a liquidized zinc coating in a process known as galvanizing. The zinc provides good corrosion resistance but is not as protective against certain elements, particularly salt, as stainless steel rope. The type of galvanizing for the wire strands, which includes, in order from least corrosion-resistant to most: electro-galvanizing, hot-dip galvanizing, and drawn-galvanizing. The specification standard for the wire rope, aircraft cable or strand governs the minimum zinc coating weight. In some ASTM standards, there are three classes of zinc coating weight outlined. For example, ASTM’s A363, A475, A586, A603 encompass Class A, Class B and Class C options.
Corrosion Resistant Steel aka Stainless Steel
Stainless steel rope has high corrosion resistance, for example, and is commonly deployed in highly corrosive environments such as marine oil and gas facilities and ocean shipping.
Stainless Steel Type 304
- Contains 18% chromium and 8% nickel
- Often used with outdoor and freshwater environments
- Appropriate for sterile environments such as medical applications
- Utilized in food ingredient processing facilities
Stainless Steel Type 316
- Contains 16% chromium, 10% nickel, and 2% molybdenum
- Often used in salt water and coastal environments
- Utilized in chlorinated pools for lap line dividers
- Installed at water treatment facilities
- Popular for architectural cable railings
The Difference Between Galvanized and
Stainless Steel Rope
Two of the most popular methods for avoiding wire rope corrosion are using strands made of stainless steel to create stainless steel rope and galvanizing the strands with a zinc coating. Both of these have pros and cons depending on the situation.
The chromium that’s used in making stainless steel has better protective qualities in environments with corrosive elements, such as seawater, which would cause galvanized steel to rust. However, galvanized steel produces better results than stainless steel rope, where metals of different types will be in contact and rubbing over each other.
Conclusion
Corrosion is the biggest threat to wire rope assemblies in the long term. It is most commonly caused by environmental elements such as oxygen, salt or industrial chemicals but can also be due to metals being in contact with each other. The effects of wire rope corrosion are to create weak points in individual strands, which eventually weaken and snap, reducing the weighted load capacity of the assembly and shortening its lifespan.
There are many methods to improve the corrosion resistance of wire rope. These include extrusion coating, lubrication, different types of galvanizing and using stainless steel wire strands. Regarding the latter two, stainless steel performs better in marine or salt-rich environments. At the same time, galvanized steel is better suited to industrial situations that would see the steel coming in contact with other metals.
At Lexco Cable, we work hard to ensure our customers get a product that will fit their needs for years, which means countering the causes of corrosion. We warehouse our wire rope indoors, in a climate controlled environment, to help promote material longevity. Our team is happy to discuss your specs to find the best, longest-lasting solution for your use and environment. Get in contact with us here.